Industries
Indoor & outdoor — Versatile HMI components for any environment
HMI components have to meet a wide range of requirements depending on where they are used. At EP Electronic Print, we develop robust and reliable solutions that are optimized for use in protected indoor environments as well as for demanding outdoor applications. Our HMI systems offer durability, precise functionality and an attractive design — regardless of whether they are used in production halls, control rooms or in the open air.
Indoor applications
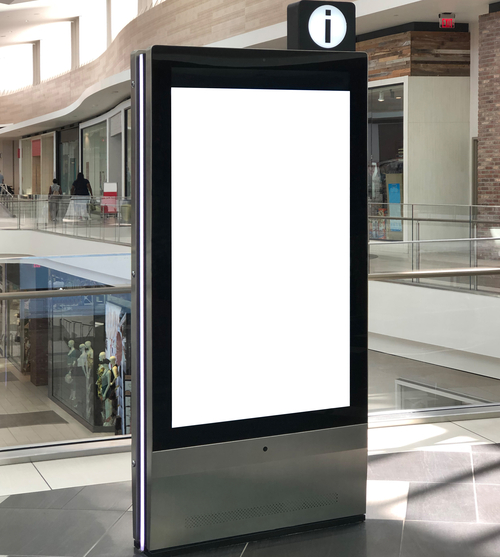
In indoor environments, the focus is on ergonomics, user-friendliness and aesthetic design. Our HMI components are perfect for applications in enclosed spaces, such as:
Outdoor applications
For outdoor applications, HMI components have to withstand extreme conditions such as temperature fluctuations, strong sunlight, moisture and mechanical stress. Thanks to resistant materials and optional coatings, our HMIs are durable and effectively protect the electronics from external influences such as dust and water. At the same time, the optimized user interfaces enable intuitive use. The displays are designed to remain easy to read even in direct sunlight and also offer high touchscreen accuracy, even with wet or dusty hands. These systems are also energy efficient to meet the requirements of sites without a permanent power supply. Their flexible integration and easy maintenance make them ideal solutions for continuous use in outdoor applications.
Our solutions are specially designed to meet these challenges and are used in:
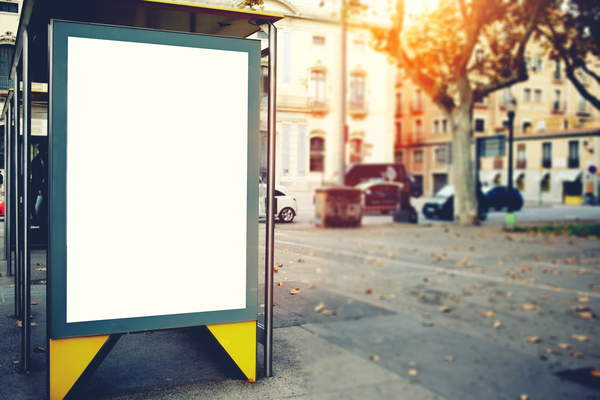
Special requirements and features
Medical technology places specific requirements on the components used to ensure optimum functionality and patient safety. Our solutions meet these requirements through:
Closed surfaces
Medical devices have special requirements in terms of reliability and the protection of users and patients. In order to avoid malfunctions due to the ingress of solids or liquids, medical devices are normally designed with closed surfaces or, in the case of medical devices, at least the IP-Schutzklasse 65 gem. ISO EN 60529 recommended.
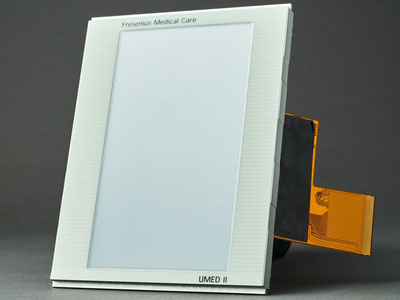
Resistance to disinfectants and cleaning agents
Frequent cleaning and disinfection is a permanent challenge for the materials used. The materials we use have proven themselves in practice over many years and therefore represent a safe basis(DIN 42115). Sometimes, however, applications require special cleaning agents (e.g. highly alkaline or acidic). We will be happy to support you with additional data on various resistances or suggest a suitable solution.
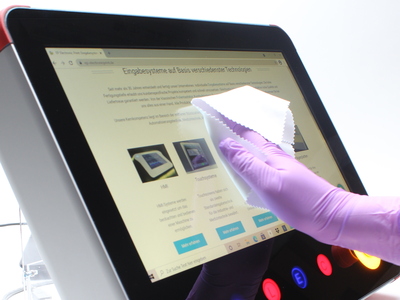
Optimized readability
Depending on the application, the readability or accuracy of the representation on the display can be a very sensitive issue. The choice of the right components, the right optical specification and the type of connection (e.g. optical bonding or air-gap bonding) must be selected with a view to the target. Neither “overshooting the target” nor “just doing it” are optimal in terms of price, quality and performance.

Traceability of the functional components
The demands on quality management are constantly increasing and have therefore led to increased safety for patients and users. If problems do occur despite precautionary and risk management measures, complete traceability of the functional components is required in order to analyze problems accurately. We can provide you with the necessary data at serial number level.
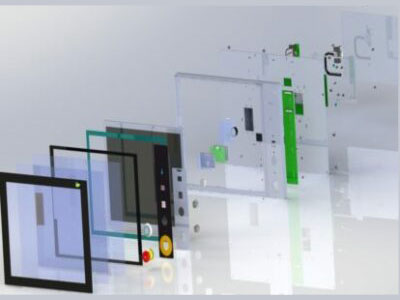
Protection against liquids
Thorough cleaning and disinfection of devices is more important in the medical sector and therefore takes place more frequently than in many other applications. Systems in medical technology should therefore be completely resistant to the penetration of cleaning agents and disinfectants, drugs, steam or water. For medical devices, at least the IP-Schutzklasse 65 gem. ISO EN 60529 recommended.
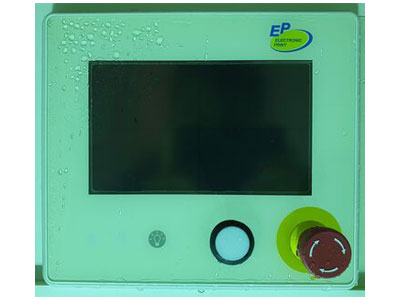
Electromagnetic compatibility — EMC
To ensure patient safety, IEC 60601–1‑2 specifies increased requirements for the EMC behavior of medical devices. This affects factors such as interference and radiation, conducted coupling, etc. The importance of the right concept with the selection of mechanical and electronic hardware cannot be emphasized enough. In the worst-case scenario, there is a risk of reworking the final device.
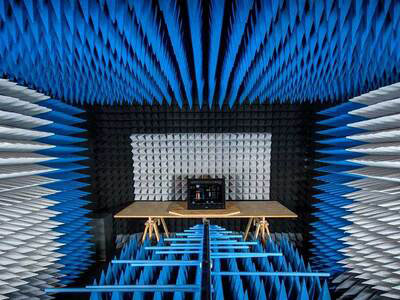
Usability with gloves
The use of gloves is common practice in all medical areas for reasons of hygiene. The latex disposable gloves frequently used in medical technology are no problem for any of our input systems and can be used without any problems. However, thicker gloves made of various materials such as cotton or nylon can also be considered if required.
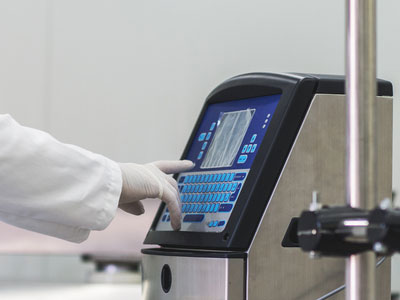
Mechanical resistance of the surface
Modern multi-touch HMI systems are usually equipped with a stable glass surface and are therefore already very robust against mechanical impact from the outside. But even if glass cannot or should not be used (e.g. for tactile feedback), we only use films with hardened surfaces (3H or 9H according to ISO 15184) and thus maximize the mechanical resilience.
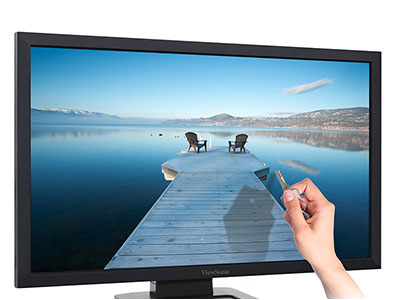
Anti-microbial surfaces
Microbes, especially bacteria, are a persistent problem in applications with high hygiene requirements. We can therefore offer the option of an anti-microbial coating for our products. This reduces the microbial load by 97% within 24 hours(ISO 22196). Although this does not replace regular, professional cleaning, it drastically reduces the risk of microbial spread.
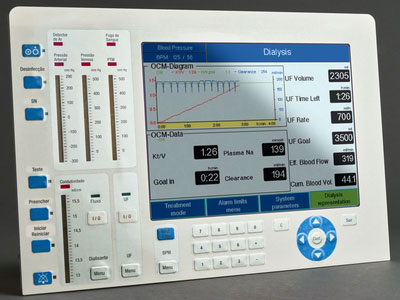
Manufacturing
ISO 13485 is a harmonized standard that formulates the requirements for quality management (QM) and the QM system of medical device manufacturers. We are happy to supply medical device manufacturers who manufacture in accordance with this standard and also provide you with all the necessary documents and information.
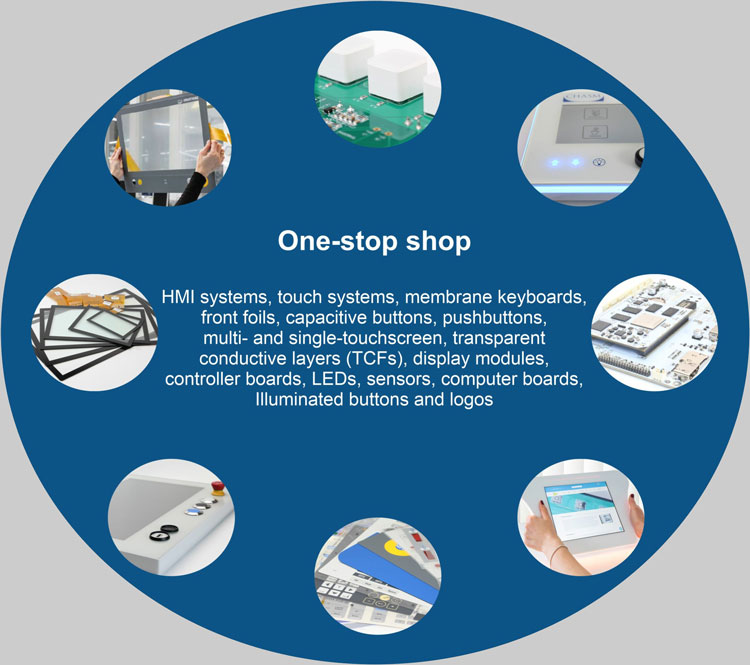
Why EP Electronic Print?
At EP Electronic Print, we rely on state-of-the-art components and technologies to develop innovative and customized HMI solutions.
Do you have any questions or would you like to find out more about our HMI solutions?
Our team will be happy to advise you and work with you to find the best solution for your project. Use our contact form or call us directly — we look forward to hearing from you!
Non-binding contact request
Am Weidegrund 8 & 10
82194 Gröbenzell Technische Anfragen:
Telefon: +49 (0)8142 /420896–20
E‑Mail: projekte@ep-electronicprint.de Allgemeine Anfragen:
Telefon: +49 (0)8142 /420896–0
E‑Mail: info@ep-electronicprint.de